BusBar Trunking System
- Home
- Solutions
- MEP Solutions
- BusBar Trunking System
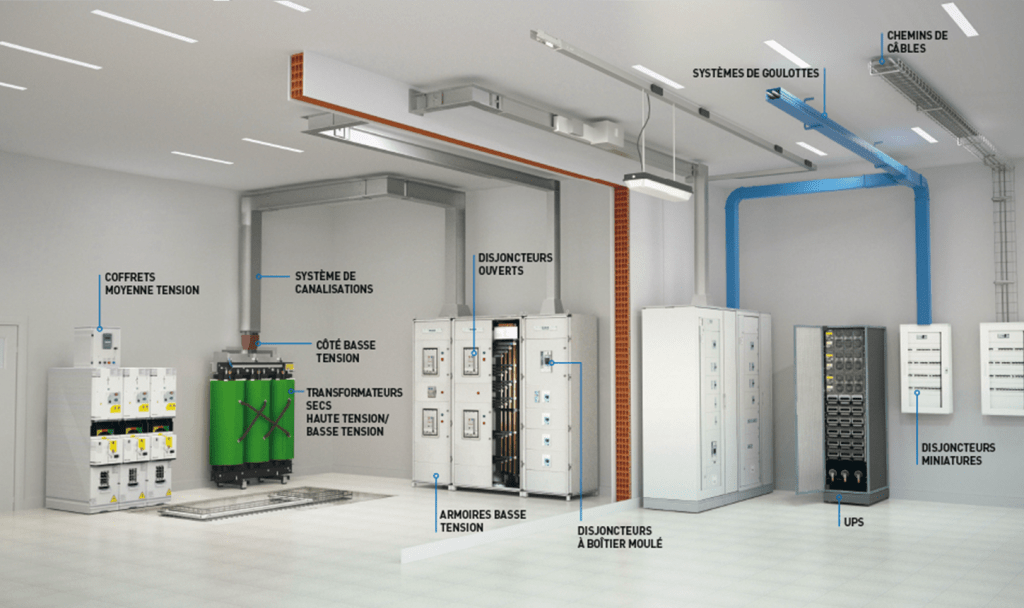
A BusBar trunking system is basically a metallic conductor, usually, as the name implies a bar or strip. This is typically used to conduct a high current, low voltage power supply. Bus-Bars are used because of their low complexity, simplistic design and maintenance. The system layout usually involves multiple bus-bars running through a building space in walls. This is due to their relative high strength and gives an opportunity to sufficiently cool it effectively.
Bus-bars are generally uninsulated and run “naked” through their storage space. While posing a high risk of electrocution, this gives rise to ease of access when compared to insulated wires as any measurement, assessment or error diagnosis can take place easily.
Trunking system uses and applications
Bus-bars are generally needed and used in;
- Large or many electrical outputs.
- Power Distribution for a large factory.
- Electrical Main in a high-rise building to branch off to individual floors.
Bus-bars systems come in many shapes and sizes, with the main factor being is how much power is to be transmitted. This requirement will alter the dimension of the bus-bars, with a common rule of thumb being that 0.7 to 1.2 Amperes per 1 square millimetre of material. Other factors can include the aesthetic look, storage space or even possible upgrades in the future.
BusBar Trunking System Advantages
Bus-bars are becoming more common by the day. This is due to their straightforward advantages, which include;
- Material, Labor and Overall cost savings.
- Future upgradeability and Flexible modifications.
- Compact Design.
- Heat Absorption.
- Resistance to the natural elements.
- Energy efficient due to low losses.
- Low Electromagnetic field (easier and safe to use around sensitive electronics).
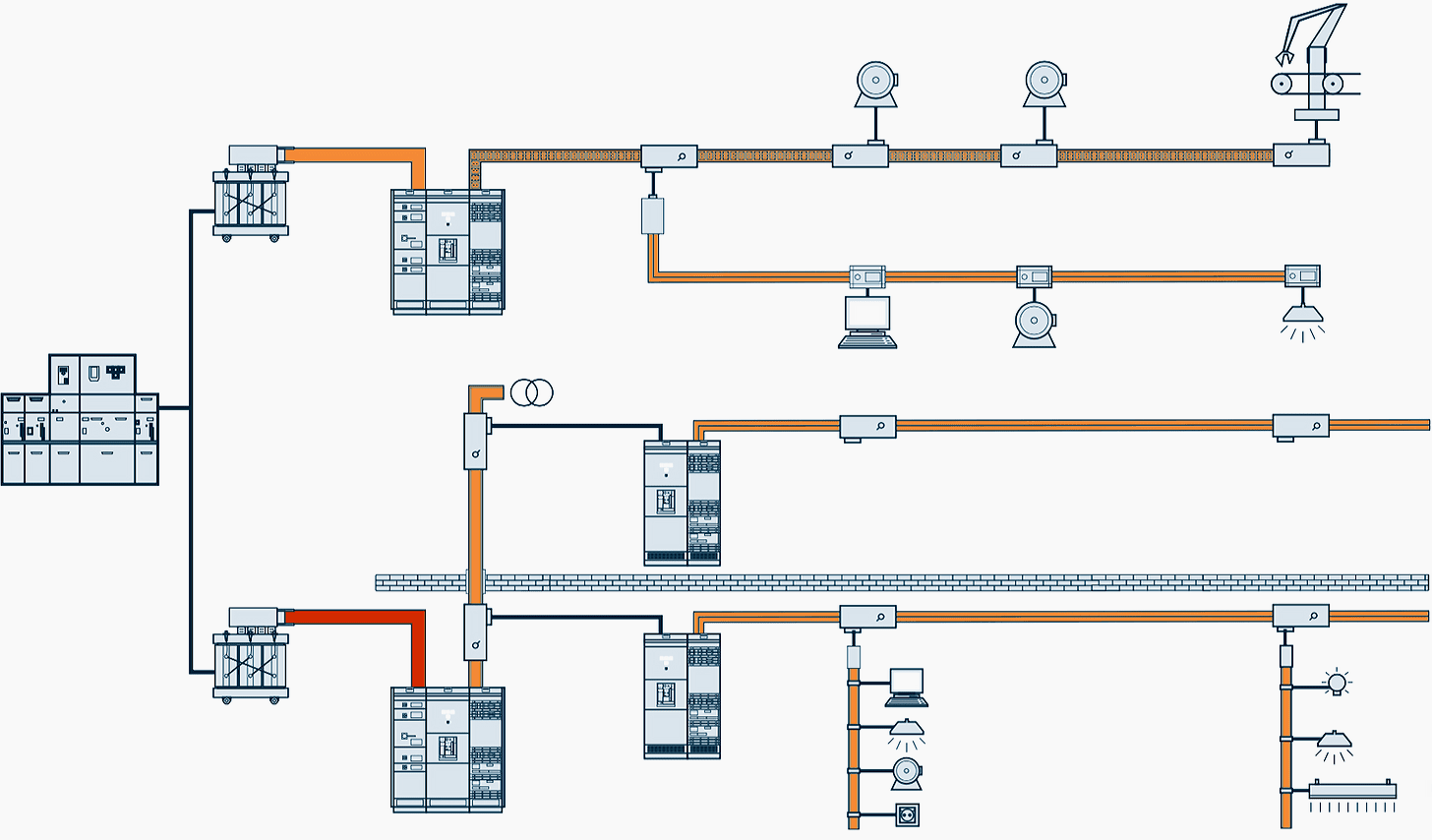
Comparison to Standard Cabling Systems
Cables are generally hectic to work with, especially if it is of great length. The improper management of cables could cause unpleasing aesthetic looks, complicated diagnostics and an overall mess when dealing with them. Cables also cause a greater voltage drop when compared to bus-bars of similar lengths. This causes a noticeable power loss across time and distance of cabling.
Cable runs often need support or to be strapped tightly to avoid slack. This means that for a specific length between cables and bus-bars, a cable needs more support per meter length used. A cable is usually more prone to the elements such as wear and tear, rodent invasion or just degradation over time. This calls for rigid support and protection over the cables which eventually increases the total weight of the system and lower space efficiency.
Other drawbacks of cables include;
- Lower fire protection.
- Not flexible (cables are harder to bend sharply).
- A higher number of points of failure (more joints and components).
- Heavy Labor needed.
- Many special tools are needed.
Bus-Bars General Design
Bus-bars are generally made of aluminium, copper or brass. An alloy mixing two or more could be used but commonly a single metal is used to keep manufacturing costs down. The dimension of the bus-bar determines the overall safe current that could be carried across, this could vary between different systems.
Bus-bars could be a simple rod, flat strip or a solid bar. The shape generally means how efficient a bus-bar or how good at dissipating heat it is.
Bus-bars connections can be easily bolted or welded together. These give great flexibility in mantling and dismantling the system. Bus-bars could also be flexible or rigid connections based on their intention of use.
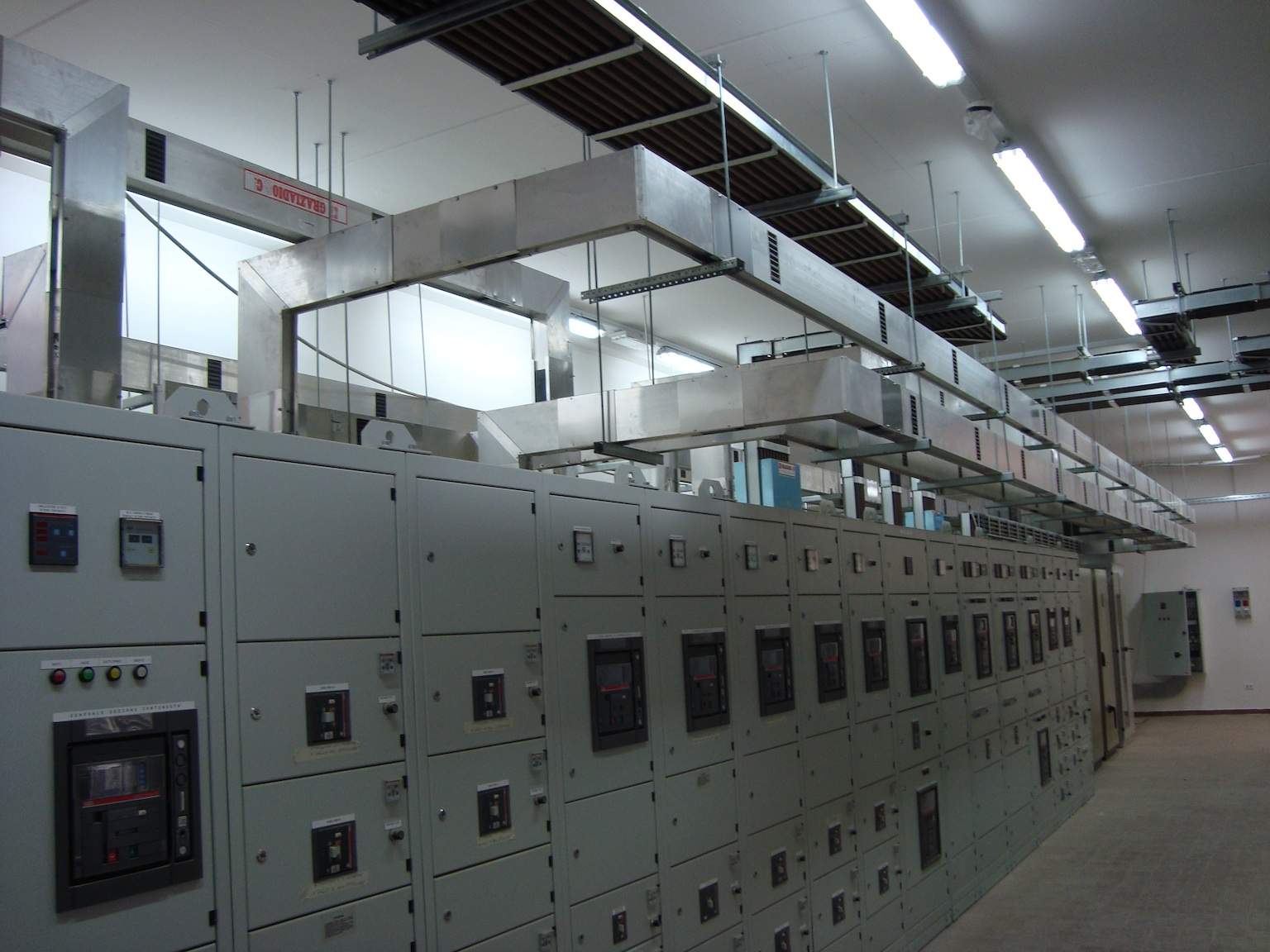
Maintenance
Bus-bars carry a high current energy flow and to describe touching a live wire as a “shock” is a severe understatement. If an uninsulated and bare-handed person touches a live bus-bar, immediate death is inevitable. Only professional entities work around bus-bars and various safety factors should be implemented to avoid loss of human life and electric fires.